Webinar Recap: Introduction to Precast Architectural Concrete

As an architect, engineer, general contractor, developer, or project manager, you want the best of the best for your client. Your next project should be durable, sustainable, and cost-effective. You may think you know architectural precast concrete, but our AIA-certified webinar will give you the tools and confidence to consider precast concrete for your next project.
We’ll further expand your knowledge on the building envelope system, precast concrete benefits, your design options, and the different PCI certifications. If you’re interested in gaining AIA credit for the course and speaking in real-time with one of our experts, register for the next webinar.
Building Envelope Systems to Choose From
There are three different types of building envelope systems you can choose from with precast concrete: wall panels, architectural facades, and rainscreens. They all have distinct qualities that will give you a variety of options for your precast concrete structure.
Wall Panels
Precast concrete wall panels can either be loadbearing or non-loadbearing. Loadbearing wall panels are typically used for schools, student housing, or data centers. While non-loadbearing walls are used more for an enclosure system and attached to a superstructure.
Choosing wall panels as your building structure will allow for more interior space within the building. This type of construction uses fewer beams and columns, so there is flexibility and opportunity to lease or use more of the space.
Wall panels can either be solid or insulated. Solid panels can absorb or reflect heat and save you costs on your HVAC systems and utilities. This is especially important when you are in an urbanized area and have to consider the heat island effect.
Insulated precast concrete panels are usually slightly bigger than solid panels and come in three different options with differing R-values.
- EPS: r5 per inch
- XPS: r6 per inch
- Polyiso: r6 - r6.5 per inch
Your insulated panels can either be held together by a carbon fiber grid or a pin system. Whichever you choose to insulate your panels with, neither will negatively affect the thermal efficiency. The exterior finish can be different from your interior finish mixture, which can then be directly painted on. This combination will ultimately save you time and money on materials and labor.
Architectural Facade
This type of cladding is a little bit smaller than wall panels and is best used for hospitals, high-rise buildings, offices, and mixed-used buildings. Since these are not loadbearing material, the architectural facade is tied back to a steel frame.
Rainscreens
Rainscreens are the thinnest option you can choose with precast concrete. Because of this, architects will have to specify the backing system, insulation, and framing member as well as the concrete mixture. Additionally, this type of building material is not waterproof, unlike wall panels and architectural facades, so you will need a moisture barrier.
Three critical components make rainscreens a success.
- Air space between the exterior cladding and moisture barrier.
- A clear drainage plane behind the exterior cladding.
- Drying of the assembly through convection.
Although this material is thinner, it is still built with high resistance and durability in mind. High Concrete Group has created an innovative concrete mixture, ThinCast, that can even be customized in design, color, and size.
6 Precast Concrete Benefits
When compared to other building materials, there are endless benefits to precast concrete. Through the physical materials, job site safety, cost allocation, and production schedule, you’ll learn that precast concrete will save you time, money, and additional repairs down the road.
1. Versatile Wall Systems
When looking at the different types of wall systems you can choose for your next project, two of the most popular ones are brick and block and cast-in-place. Although they are good options, precast concrete solves a lot of problems that come from using these common wall systems.
Building with brick and block comes with a labor-intensive job site since masons will have to individually lay down bricks, stone, or concrete. For both brick and block and cast-in-place, workers will have to put in waterproofing and stud the walls after construction.
One of the major downsides to brick and block is these buildings have low resistance and are more susceptible to seismic damage. This could be potentially fatal depending on what the building is used for and its location.
On the other hand, cast-in-place requires a lot of workers as well because everything happens at the job site. This building material is also limited in its facade features and design flexibility.
Precast Concrete
Precast concrete is constructed in a controlled, plant environment which means fewer labor costs and better job site safety. The concrete will be formed and poured well before it needs to be on the site, so it is a more efficient system compared to brick and block or cast-in-place.
2. Enhanced Jobsite Safety
As mentioned above, precast concrete will increase job site safety throughout the entire process. Since the concrete is formed in a separate environment, you won’t need as many people on location. Along with that, you also won’t need scaffolding which reduces the risk of falls and injuries.
When more people are at the site, it increases the risk of injury, poor quality control, and project errors. There is also a higher chance of logistical and scheduling errors because not everyone can be at the site at once.
Precast concrete plants can also put windows and electrical boxes directly into the molding so you can remove that extra step at the job site.
3. Built with Durability in Mind
Concrete itself has great compressive strength but has a low tensile strength. Over time, your building will naturally see cracks from this tension. To combat this, precasters use mild steel reinforcements like welded wire or mesh.
Long-term, more serious cracks can be reinforced with prestress strands or steel cables that run from each end of the form. Because of this, we can create longer panels so less material is used and labor, shipping costs, and crane picks are minimized.
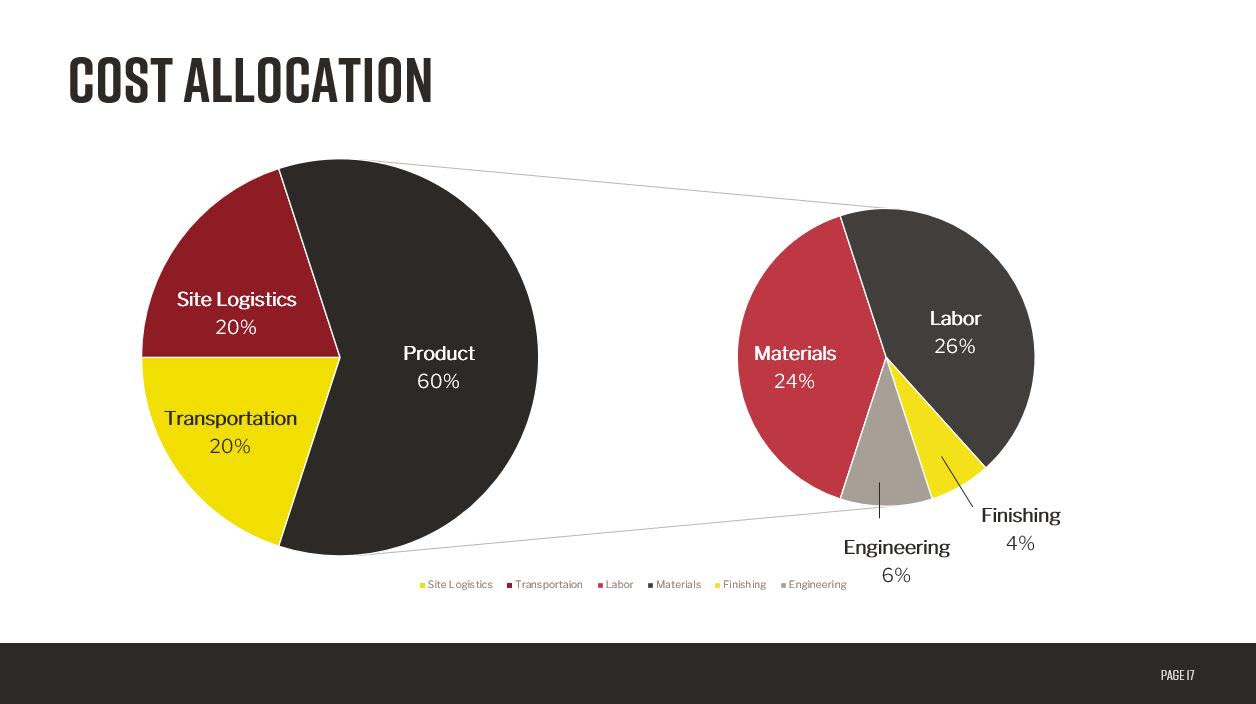
4. Get the Most Out of Your Budget
The way the costs are broken down for your precast concrete project holds several benefits for your organization. Your cost is allocated into the following categories
- Product - 60%
- Transportation - 20%
- Site Logistics - 20%
Within your product budget, you can break it down even further.
- Labor - 26%
- Materials - 24%
- Engineering - 6%
- Finishing - 4%
It’s important to note that only 4% of your cost will be allocated to finishing. Precast concrete finish options are endless and customizable. This small portion of the budget can take you from a simple building to one that is made unique to your organization.
5. Minimal Panelization
Choosing the right kind of panelization can save you huge amounts of time and money. Vertical wall panels made with precast concrete will give you the least amount of material and be the same height as an infill building.
With a vertical wall panel, the building will need 3 to 5 panels in comparison to 11 with other panel types. And fewer panels will save you money on materials, as well as transportation costs. Consider the amount of transportation needed to ship 3 to 5 panels versus 11 panels.
6. More Efficient Offsite Construction Schedule
The precast concrete construction process can be broken into 5 sections. The main benefit of this schedule is a majority of the phases are happening at the precast concrete plant, instead of the job site.
- Sales/Estimating. During this phase, a precaster will ask you questions about the design of your structure and then provide you with a cost estimate.
- Engineering. Engineers will design all the connections, reinforcements, and loads.
- Production. We’ll then work on creating your molds and stripping the product. We’ll batch the concrete to ensure it flows at a good pace and then consolidate it to remove any air bubbles. Once complete, it will be stored at the precast concrete plant, until the job site is ready for the material.
- Shipping. Your structure panels will be shipped to your building location. Precast concrete plants will only work with job sites within a certain radius so there aren’t excess transportation costs or delays.
- Erection. Finally, at the job site, the precast concrete panels are sealed and caulked at the joints.
These six precast concrete benefits above will allow your organization to save time and money while building a structure that can withstand the toughest conditions.
The Sustainability of Precast Concrete
Precast concrete is one of the more sustainable building material options for your next structure. It is built with resilience and durability in mind. While other building materials have a lifespan of 30 years, precast concrete is meant to last up to 100 years.
Depending on the location or industry you’re in, having a structure that is resistant to natural weather disasters and explosions is essential. Precast concrete is wind, blast, seismic, and fire resistant so you can feel safe within your environment.
Precast concrete is built with edge-to-edge insulation which increases its R-value as well as its thermal efficiency. Additionally, you can opt to include a green roof on the top of your structure to further reduce temperatures inside your building and the surrounding area.
When applicable, supplementary or recyclable materials are used within the concrete mix to help reduce carbon emissions. This depends on the mix, design, and location of the concrete mixture within the structure.
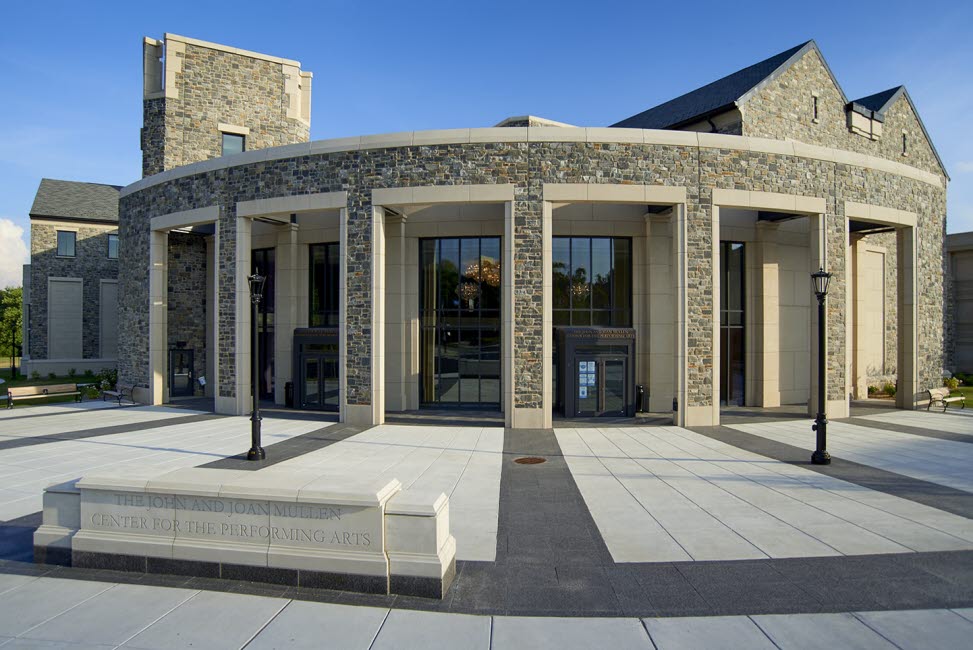
The Design Flexibility of Precast Concrete
As mentioned in the cost allocation, approximately 4% of your budget will go towards the precast concrete finish. You’ll notice that the design of precast concrete structures comes with unique opportunities for organizations to incorporate their brand and own design into the building.
Applied Finishes & Textures
During the Architectural Precast Concrete webinar, we highlight the different finishes and colors available to you.
- Acid Etch Finish. A shiny, sparkly effect with different levels of wash. We recommend a medium wash to give you the most consistent finish on your structure.
- Blast Finish. Similar to an acid-etched finish, with a more sandy look to it. This option also comes in a light, medium, or heavy wash.
- Exposed Aggregate Finish. The process of this finish keeps the cement from hardening to show mostly stone.
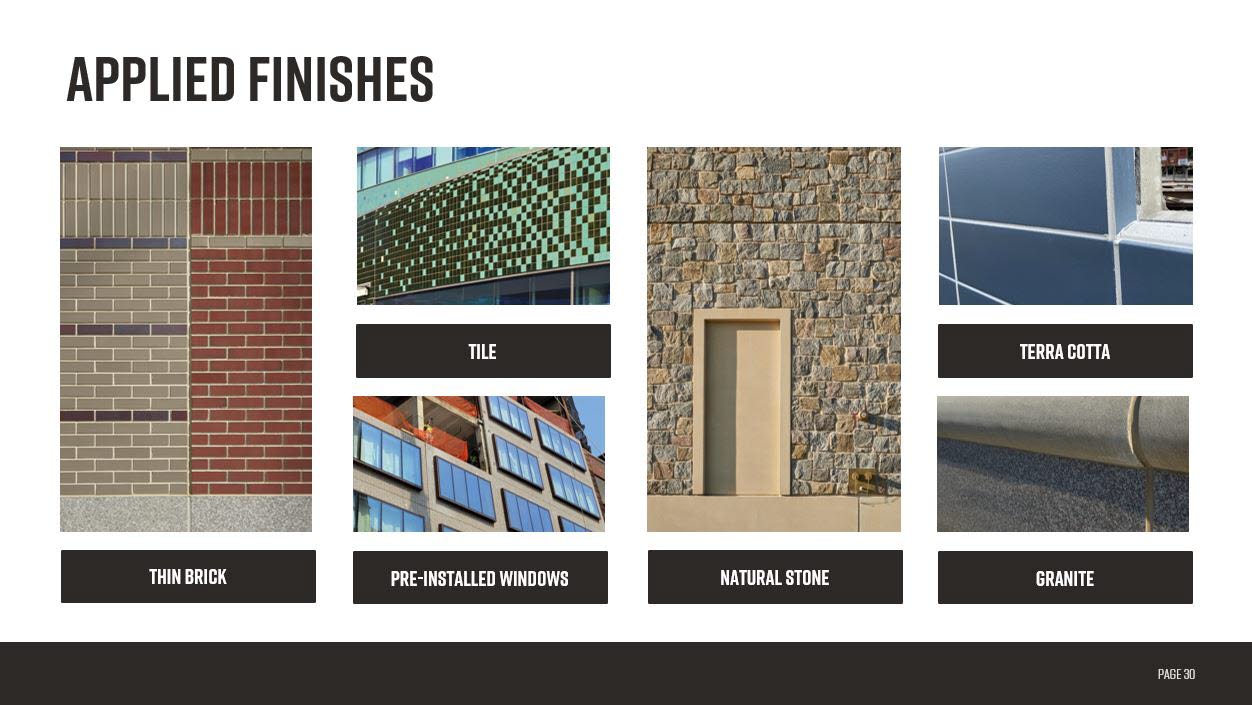
Going one step further, you can decide on several different applied finishes like brick, tile, natural stone, terra cotta, or granite for your structure. If mentioned early enough in the process, a precaster also can pre-install windows into the mold to further reduce the labor needed at the job site.
Once the textures and finishes are decided, you can truly make the building your own by adding emblems, text, revels, and form liners to the exterior. Logos can be made with a rubber liner and a piece of insulation to fit into your mold.
PCI Certification: What to Consider When Vetting a Partner
When deciding what precaster to choose from, we recommend looking at their PCI certification. There are 4 levels, that a precast concrete plant can earn, the highest being AA. An AA precast concrete plant is audited every year and adheres to high standards of work.
Below, we will describe the four levels of architectural certifications.
- AD - This precast plant can make a single color, flat panel.
- AC - The next level gives plants the ability to form surfaces, liners, and revels.
- AB - Just below an AA standard, AB certifications can produce multiple colors and textures and must produce a 3-D drawing for you before the project begins.
- AA - The highest standard, can do all features of the lower certifications but the precaster must participate in project surveys and plant audits.
High Concrete Group is proud to have earned an AA architectural certification, meaning we can produce any level of project, from AA to AD. This also means we are consistently testing the concrete, providing mock-up panels for our clients, and retaining records of past projects.
Get an in-depth introduction to architectural precast concrete.
