Warehouse Layout Design for Efficient Operations

In a previous blog, we talked about designing your warehouse with precast concrete and the benefits that come with using this building material. But what’s the connection between your exterior structure and the interior layout? Does the exterior of your warehouse have an effect on the operations?
Below, we’ll define important warehouse layout design objectives and how precast concrete can help maximize space and optimize efficiency in your facility.
The Five Objectives of Warehouse Design
As you begin to design your distribution center or warehouse, there are a lot of considerations. These factors can be categorized into five main layout objectives. And with each of these objectives, you’ll find that precast concrete can be a great benefit to you as well.
#1. Optimize the Interior Space
This is probably the most important aspect to consider because the interior space of your warehouse and the flow of traffic is crucial to your success. As you’re looking at your inventory, machinery, and storage space, you have to make sure there’s an interior capacity to work efficiently.
There are quite a few warehouse storage layout designs you can choose from, including
- Single aisle warehouses.
- Multi-aisle warehouses.
- Drive-in warehouses.
- Flow warehouses.
Whatever design option you choose, your choice shouldn’t be minimized due to limited internal space.
The Precast Concrete Benefit: Precast concrete panels are load-bearing, which means the weight is transferred from the roof, floor, and lateral loads to the foundation of your structure. This benefits you in two ways, your structure is incredibly durable and long-lasting and the need for interior columns is eliminated.
With little to no interior columns within your warehouse, you have free reign to design a flow of traffic that optimizes your productivity, holds more inventory, and better operates your machinery.
As a result, precast concrete panels provide your organization with flexibility in how to design your warehouse layout.
#2. Be Flexible for Changes
Whether the change comes through production flows, inventory levels, or seasonality factors, your warehouse needs to be adaptable. The growth of your warehouse, when necessary, should not be a hindrance to your production.
The Precast Concrete Benefit: This versatile building material allows you to easily adapt and add to your warehouse when necessary.
If you find that you’ll need more than just an addition, maybe an entirely new warehouse, precast concrete can quickly be constructed and erected so you can continue maintaining a profit. Compared to other construction materials, like steel, precast concrete structures are consistently completed twice as fast.
Another great advantage of precast concrete construction is that it happens year-round. Weather delays are virtually eliminated in a precast construction timeline. Once your panels and building components are produced, they will be transported to the site and installed adeptly.
And if this is for a warehouse expansion project, precast concrete construction methods mean there’s less disruption for the flow of work and production in your existing structure.
#3. Protect Your Inventory & Employees
The processes and products within your facility are what bring success to your supply chain and organization. As you’re considering your warehouse design, ensure you’re being proactive about product and employee safety.
The Precast Concrete Benefit: As an extremely resilient building material, precast concrete can withstand natural disasters, high moisture environments, and the natural wear and tear of warehouse operations.
Also, depending on what you’re storing in your warehouse, you can have a heightened level of protection by using precast concrete. Having the ability to better control indoor temperatures decreases the risk of damage or destruction of your inventory.
This is a key characteristic when planning your cold storage warehouse design. Products that need cold storage such as pharmaceuticals or food products, need a material with a strong building envelope so temperatures aren’t fluctuating and there aren’t increased energy costs.
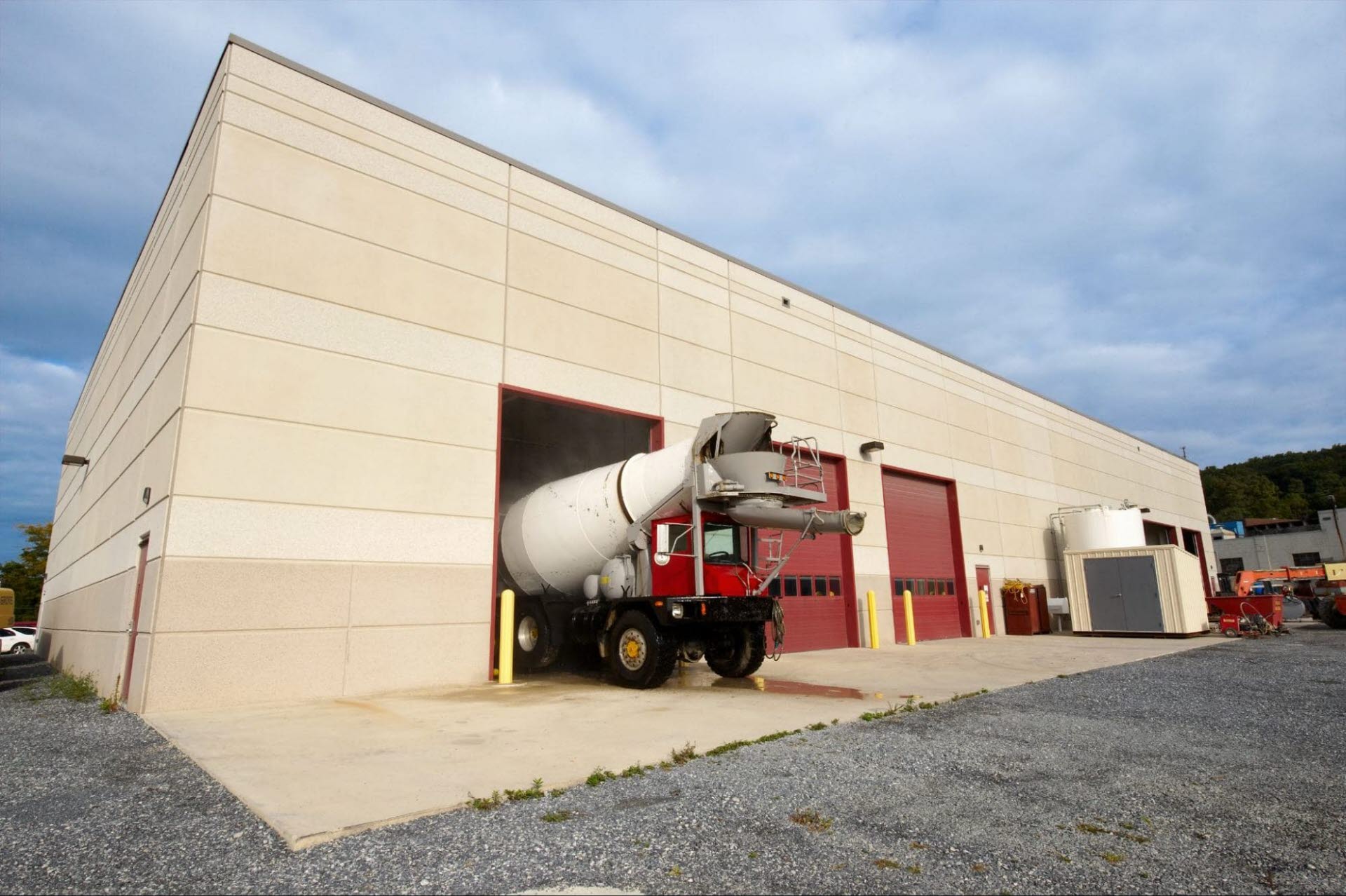
#4. Build the Design You Need Without Overstretching Your Budget
Just based on the characteristics in this blog alone, there are a lot of considerations for your warehouse layout design. To further expand on this, your budget should not minimize the needs and wants for your new warehouse design.
Within the construction industry, you’ve probably experienced a lot of cost fluctuations between materials, transporting goods, and labor. Now more than ever, it’s difficult to ensure you’re meeting all your building needs and wants and staying within budget.
The Precast Concrete Benefit: As we mentioned above, precast concrete is produced in a controlled facility, which leads to more stability in the cost of the project.
By repeating patterns and reusing molds and liners, you not only get your project done more efficiently but save costs. That way you’re not spending money on additional materials. Our formliners expand your design abilities, rather than constrict them.
As an additional bonus, your cost savings are going to go beyond initial production. Since precast concrete has such a strong building envelope and high thermal efficiency, you’ll save money on heating and cooling costs within the warehouse.
#5. Keep Your Facility Secure
The final objective to consider is how your warehouse layout design ensures security and protects your inventory. You hold a lot of valuable machines, equipment, and inventory within your warehouse, and the design and layout should warn off unwanted guests.
The Precast Concrete Benefit: Precast concrete has incredible strength and durability. In cases where other construction materials start to deteriorate from water and moisture, concrete actually grows stronger. And when a building remains well-maintained, it’s less likely to be disturbed and invaded by unexpected intruders.
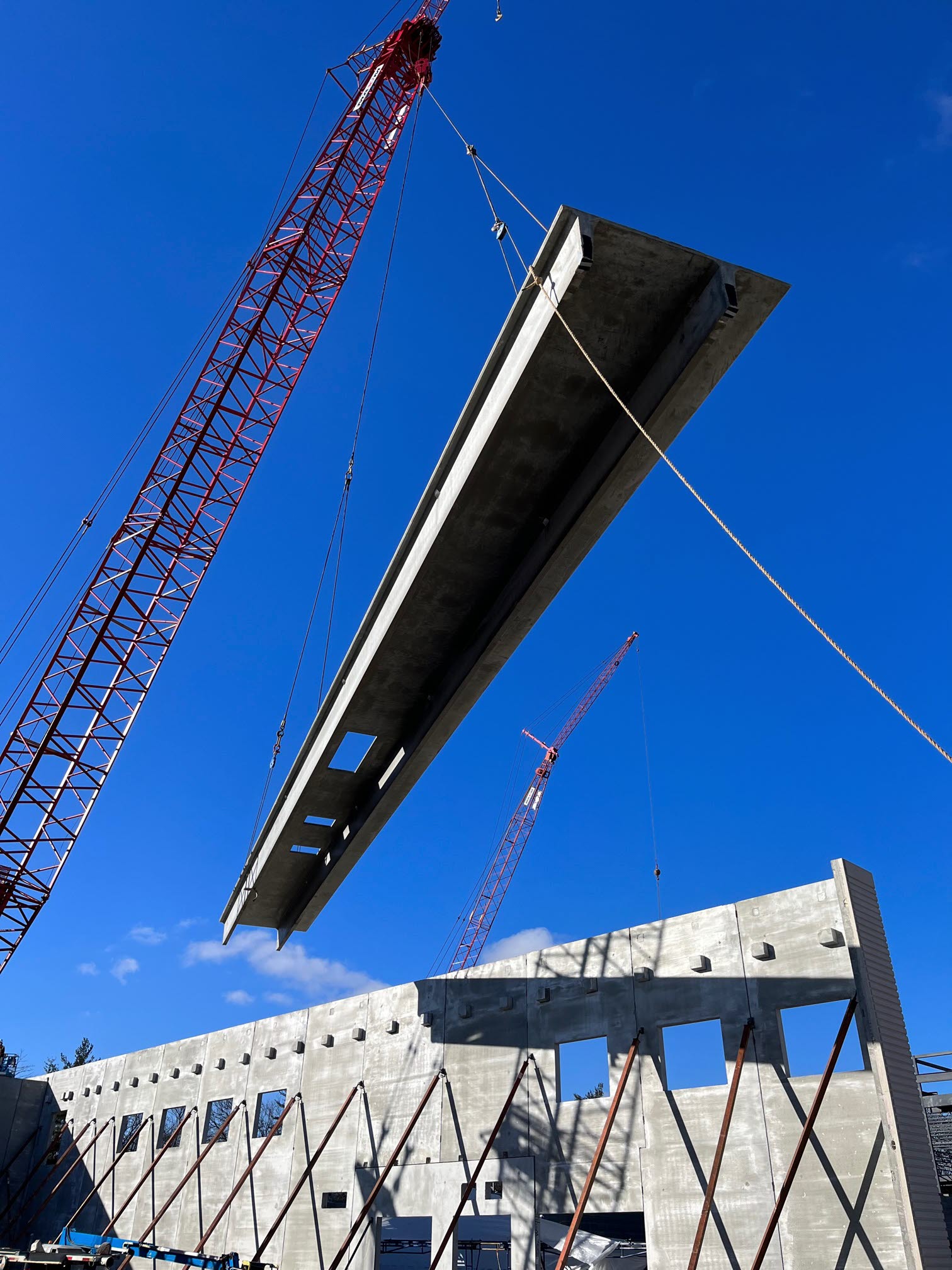
Different Types of Warehouse Designs
Within your warehouse interior, you can arrange your racks and inventory in different ways to find the most effective flow of traffic. And since precast concrete eliminates the need for many interior columns, you have a lot more options and flexibility.
U-Shape
The U-shape layout is the most common warehouse layout design. In this configuration, the shipping and receiving ports are right next to each other so you can have shared dock resources. This can provide great benefits, but it’s important that you don’t cause congestion at each of the docks.
Within the warehouse, a U-shape design puts static storage, or inventory that sits for longer periods of time on the sides of your warehouse, and dynamic storage, or inventory that moves through the warehouse quickly, in the middle of the warehouse.
I-Shape and L-Shape
I-shape and L-shape warehouse storage layout designs are typically used in larger warehouses that offer higher volumes of inventory and storage. Whereas a U-shape design puts the docks side-by-side, these shapes will put the docks on opposite ends of the warehouse.
Both the I-shape and the L-shape designs need higher levels of security because you need to protect a larger area of entrances. Whereas the U-shape entrances are right next to each other so can be better protected with a smaller amount of security.
The commonality of all three shapes is that the dynamic storage is kept in a central location of the warehouse and the static storage is off to the sides and along the walls of the warehouse.
Maintain an increased level of flexibility for your warehouse layout design by choosing precast concrete.
