The Stability of Precast Concrete Costs in an Unstable Market

Although material and labor shortages have caused construction costs to rise, there is still a steady demand for new construction. So, how can contractors, architects, or developers combat these rising costs and still deliver a superior product?
The answer is precast concrete. Precast concrete costs are significantly more stable than other construction methods because of the way it's produced, the efficient installation process, and the consistent workforce behind the entire construction.
Recent Trends of Rising Construction Costs
It’s no secret that a wide variety of industries are facing rising costs due to supply chain disruptions and labor shortages. We saw significant spikes in construction costs between 2020 and 2021.
The United States is starting to see improvements in these construction costs in 2023, with lower increases and even some materials starting to decrease in cost. However, past years can still make you weary of unexpected fluctuations in the future.
Cost of Materials
Since 2019, a majority of construction materials have suffered from increased costs. In 2022, we saw a 19.2% year-over-year and 35.6% increase in the price of building materials since the start of the pandemic. Compared to past years, this spike is exponential.
Cost of Labor
Labor shortages also contribute to the rise in construction costs. The industry is aging and struggling to find qualified contractors to replenish the deficit. Current workers are being asked to work overtime and as a result, become burnt out.
The U.S. construction industry is currently experiencing a shortage of 430,000 workers. These shortages are because potential workers are finding less labor-intensive and higher-paying jobs elsewhere.
How Precast Concrete Costs Can Secure Your New Building Project Budget
So, how do the rising costs affect a potential building project?
When materials cost more to you, it ultimately raises the price for your client. Along with this, supply chain issues can also cause deliveries to be delayed and schedules to run longer. And in the construction world, time is money.
On the other hand, what do labor shortages mean to your client? There are multiple reasons why labor shortages can become a costly implication to your project.
First, just like delays with materials, there will be delays in project completion. Fewer workers mean things are taking more time. And as we stated above, these workers are becoming burnt out from long hours, which heightens the risk of human error.
Additionally, less qualified workers may be brought in to help fill gaps, which creates a higher risk of miscommunications and the end result being an inferior product.
How do precast concrete costs come into play? Based on the production processes of this building material and its innovative techniques, you’ll find that the cost estimation of precast concrete is more standardized and secure compared to other traditional construction methods. This will be supported through the building material itself and the skilled workers producing your panels.
Precast Concrete Building Materials Use Renewable Resources
Part of the reason there’s a cost increase in many construction materials is that they’re harder to get because of interruptions to the supply chain. With high demand and lower supply, you can expect that prices will increase.
But, with the materials that make up precast concrete, there’s less worry about manufacturing and transportation delays. A majority of the materials are renewable resources including gravel, sand, cement, and water. This means they can be found virtually anywhere and your team won’t have to suffer from deliveries being delayed.
One of the greatest benefits of precast concrete is that it’s prefabricated in a controlled environment. This process emphasizes stability and allows our precasters to be more prepared for your building project with the materials you need.
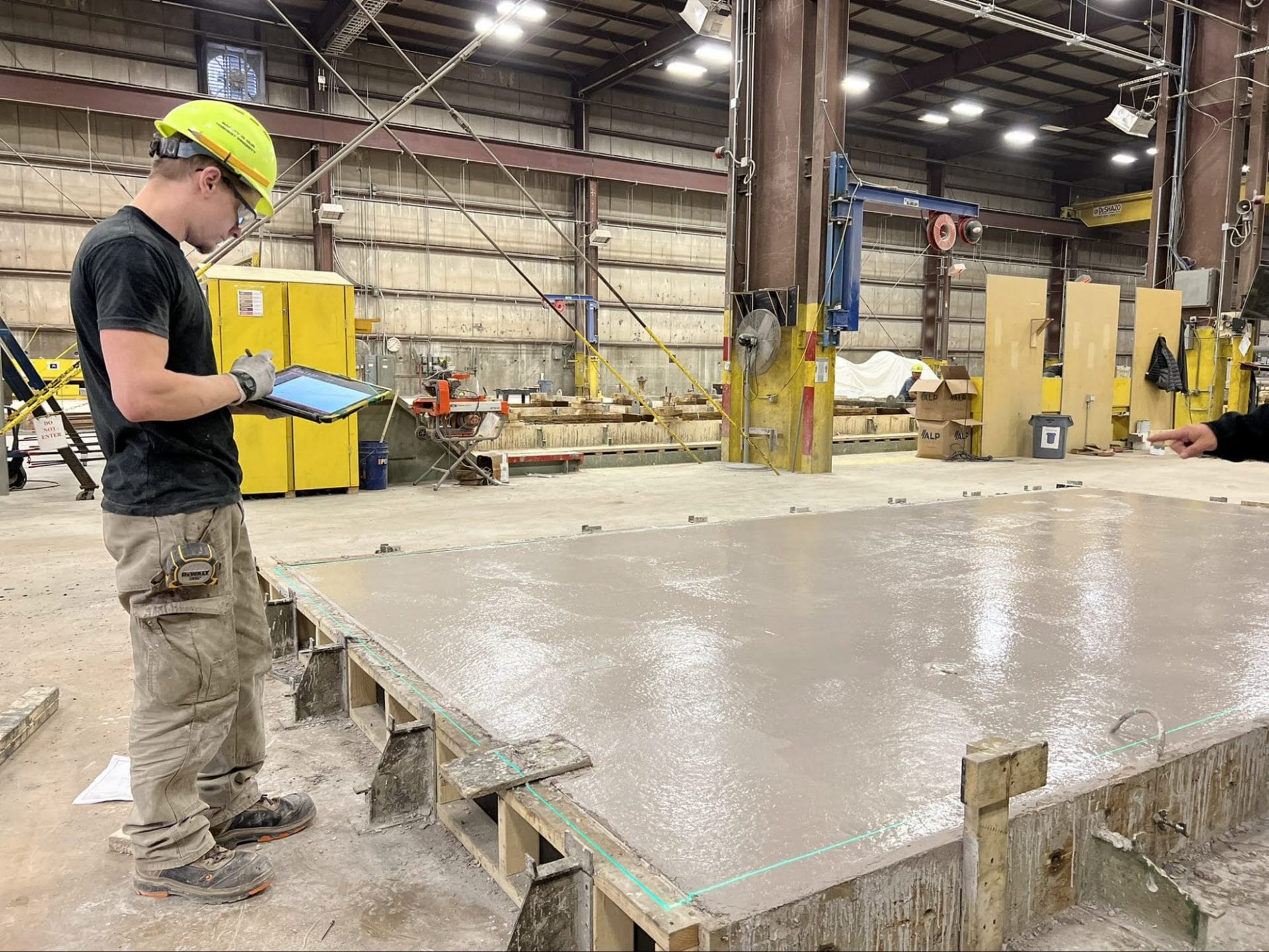
Cost Savings of Precast Concrete
Precast concrete budgets are a bit different than traditional budgets, because of the construction process. Whereas transportation and labor are a higher percentage in traditional methods, precast concrete allocates 60% of your budget to the product.
A portion of your construction budget is allocated for labor and on-site installation. In a typical construction project, labor can be up to 50% of your total budget. These costs will only continue to rise if the retired construction workers are not replenished.
However, precast concrete facilities have a consistent workforce that works strictly on precast concrete. Rather than traveling from site to site and picking up jobs where needed, precasters stay in one place and are specialized in a specific task. This also creates a more stabilized cost estimation of precast concrete.
How Precast Concrete Costs Benefit Your Role
A building project from start to finish includes a number of areas of expertise. Wherever your role fits into the construction process, you can be sure that you’re saving money and providing a more secure path for your client when you choose precast concrete.
Site Logistics & Precast Concrete
20% of your precast concrete budget is attributed to site logistics. As a general contractor or construction manager, it’s your responsibility to create a smooth process. With precast concrete, you can simplify the on-site installation process and get the most out of your budget.
At a typical job site, there are a lot of moving pieces and processes happening at once. Occasionally, these turn into miscommunications and logistical delays. And with every construction project, time is money. So when things aren’t on time or need to be redone, you are losing money.
By using precast concrete as your building material, there will be a smaller crew on the job site, which can ultimately lead to saving money and provide less opportunity for injury and human error delays.
In addition to saving time and money through a smaller crew, precasters also install multiple components to the precast concrete panels, before they are brought to your site. This includes insulation, windows, and electrical panels.
This means that the cost of precast concrete walls is more valuable because more steps are involved in the construction process. As a result, the installation process is efficient and the building will be ready for market much quicker.
Develop a Long-Lasting, Durable Structure
Resilient buildings ensure you’re receiving a greater return on your investment. Unlike other construction materials, precast concrete strengthens in the presence of moisture. When the ingredients of precast concrete are mixed with water, it creates high compressive strength rather than deteriorating.
You can be confident that precast concrete buildings will stand the test of time. They are extremely resistant to high winds, storm surges, flying debris, and severe weather. So, over time you can expect fewer building repairs or costly maintenance bills.
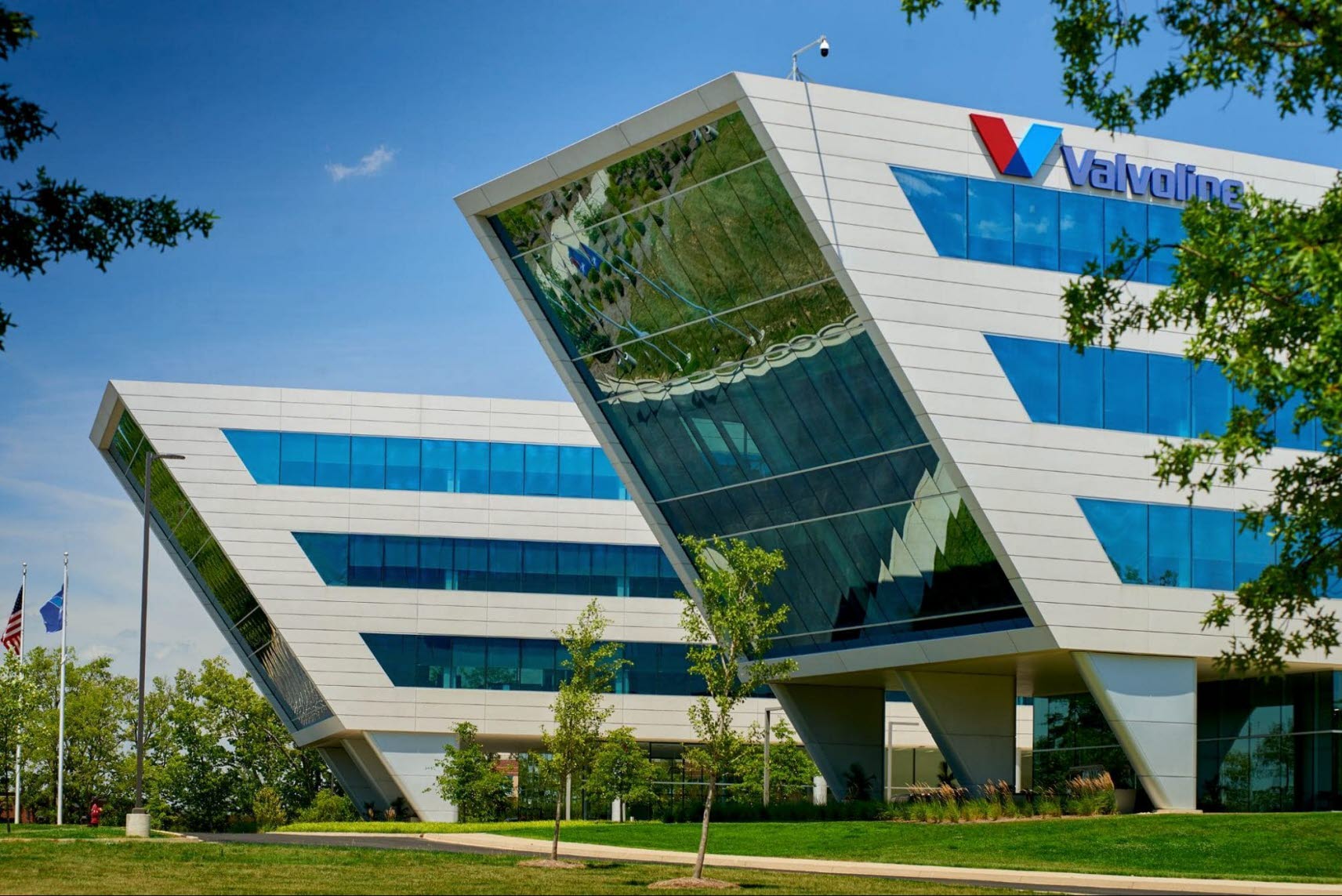
Design Flexibility, Without Breaking Your Budget
There are times when certain design features are an integral part of your building and must be factored into your budget. Or you want your building to match an organization’s campus or brand, or to stand out from the competition.
No matter the reason why you’re looking for unique design features, you shouldn’t have to sacrifice other things, expand your budget, or face unexpected costs down the line.
The foundation of precast concrete allows you to create different aggregates or different colors for your building. You can also choose between different textures that are not only cost-effective but have a simpler installation process than if you wanted to create different textures with another building material.
Take Control of Your Budget and Speak to a Precast Expert Today
