How You Can Take Advantage of Precast Concrete

The process of designing your structure, building the project, and getting it up and running involves a lot of moving parts. With operations happening simultaneously, it can be easy to miscommunicate or have setbacks along the way.
The biggest advantage of precast concrete is how it simplifies the process for you. Whether you’re the architect, engineer, or general contractor on the project, we can help you combat strict timelines, minimize road bumps, and build more sustainably.
Setting Your Building Up For Success
As you begin to picture how your structure will come to fruition, it can be hard to imagine possible setbacks or conflicts down the line. Initial blueprints and drawings may not provide the full depth of pain points or areas that need improvements.
Later in the blog, we’ll clearly define more advantages of precast concrete. When this building material is used efficiently and incorporates BIM, it helps you meet strict timelines, stay within budget, and give you design versatility.
By including a precast concrete producer early on in the construction process, they can define key features of your building that would benefit from precast concrete.
Because this is such a crucial step in the project, High Concrete offers free design assistance for your team to establish where precast concrete can enhance your overall structure.
As part of this design phase, our team will give you an idea of what precast concrete possibilities are available that keep your structure within budget and scope. Our processes allow us to have high flexibility in exterior design. The key is to repeat these patterns for not only a beautifully finished piece but also a cost-effective structure.
Our Design Assist Program
Before the design of your project is completed, a trade subcontractor is retained by the construction manager to provide design assistance to the architect and engineer. Then, the trade subcontractor carefully reviews and inspects all design documents.
The trade subcontractor helps with construction details, loading concepts, constructability reviews, product samples, and value engineering. We’ll work with the design-build team to provide loads and the structural engineer will then use these loads to complete the foundation and structure’s design.
Throughout the project, we’ll reference and analyze the design documents to ensure everything is aligned. Your team will be notified of any material differences that may negatively interfere with the design documents or increase the cost and time of the project.
Our team will also provide a cost health check during design development so everyone is on the same page and no unexpected costs or extended schedules occur. If there are significant, necessary changes, our team will provide an updated budget.
The biggest advantage of working with our precast team is we’ll provide additional knowledge of standard precast concrete best practices. This includes weight impacts and limitations, standard connections, a structural analysis, and optimum detailing and framing practices. All of this will be considered along with project economics and structural impacts related to applicable building codes.
To conclude the design process, our team will detail all precast concrete elements, and how they’ll be erected and connected. Finally, we’ll provide structural calculations that support all our detailing.
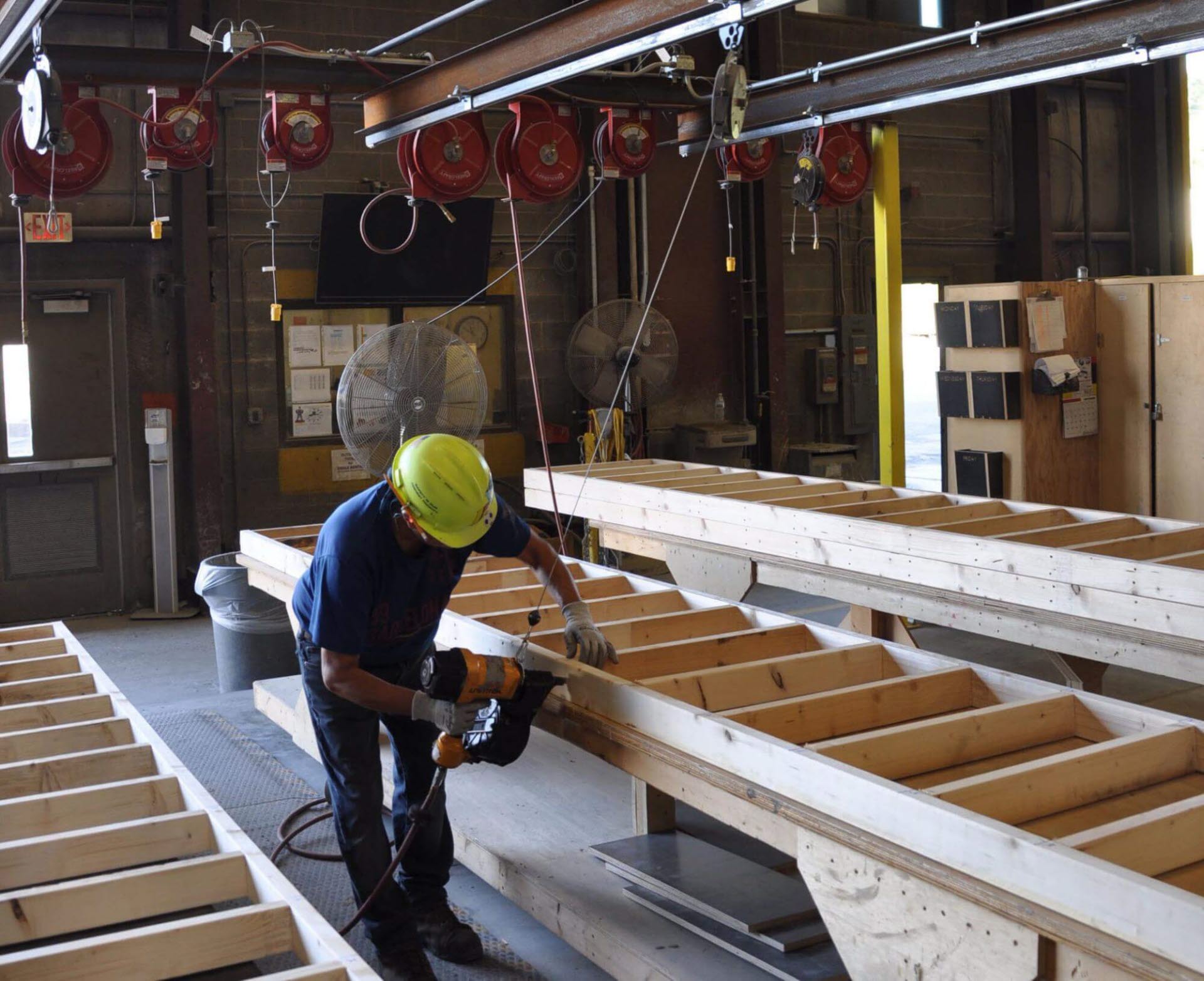
Leveraging Off-Site Construction Benefits
The advantages of precast concrete during the physical construction of your building are truly what make this material stand apart from the rest. Because of the off-site processes and how precast panels are made, there is a wide range of benefits for you and your team.
Level of Predictability
Most notably, the efficiency of assembly is heightened when a majority of the process occurs within a controlled environment. There’s a higher level of predictability and therefore a lower risk of miscommunication or human error.
Reduced Risk of Injury
Consider all the workers and machines that are on a construction site daily. Even with the safest weather conditions, construction workers are at a heightened risk of injury because of all the moving factors on-site.
However, when using precast concrete, the number of on-site labor is severely reduced. And when fewer team members are on-site, there’s less risk of injury. On average, when installing a precast concrete building, only 8 to 12 workers are needed, depending on the size of the project.
Simultaneous Construction Activities
Because your building won’t be transported until it’s ready for installation, your team can get the site ready for erection, while we’re producing your building. This gives more flexibility if delays occur during either process.
Improved Sustainability
By 2025, construction waste is expected to total 2.2 billion tons. This is because up to 30% of materials that are brought to a job site end up in landfills and as waste. These statistics are frightening to those looking to reduce their environmental footprint.
The benefits of precast concrete go beyond your project but also contribute to a greener future. The controlled facilities allow us to minimize waste during the construction process, and bring almost no waste or debris to the job site.
Also, other factors that are harmful to the environment and are typically associated with construction sites, including various pollution types, high levels of dust, and increased traffic congestion are greatly minimized with precast concrete.
Increased Quality Control
The systems and processes of precast concrete construction ensure high-quality results and precision at each step. Our team will conduct a post-tension and pre-tension test to strengthen the concrete and make it more durable long-term.
As a bonus, all precast concrete facilities can apply to be PCI-certified, which is awarded to precast concrete producers who meet innovation, quality, and design standards. High Concrete is ‘AA’ certified, meeting the highest standards.
Ready for Market Sooner
Delays and logistical errors are almost inevitable for a construction project. When they occur, timelines can be elongated and budgets can be pushed. The security of precast concrete processes gives a more definitive timeline from the beginning so your structure is ready for market sooner.
Along the same lines, once your precast concrete building is ready for installation, the erection could only take a few days, depending on the size of the structure.
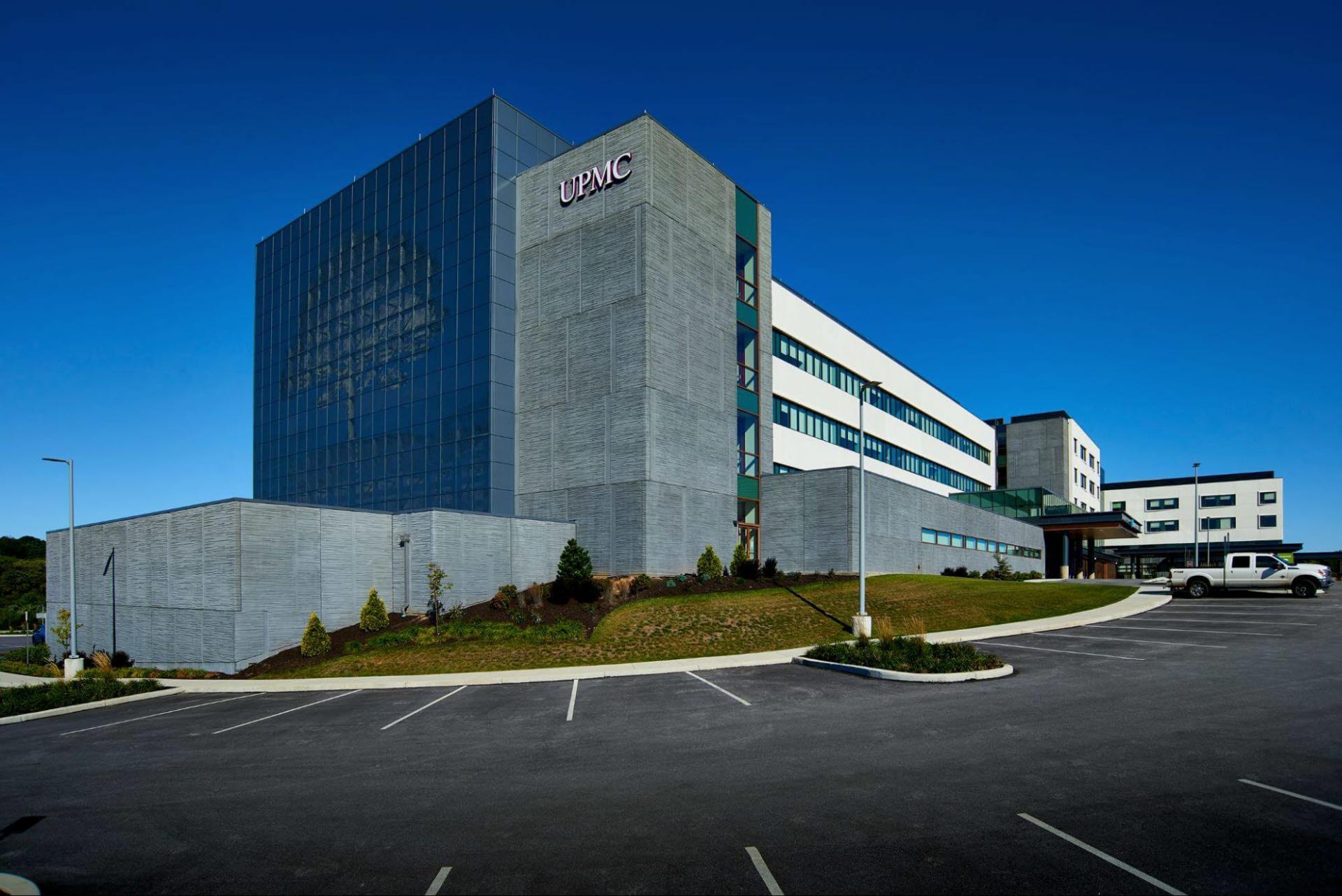
Providing Resilient Benefits to Your Clients
At the end of the day, everyone wants to provide a high-quality product to their consumers. Customer satisfaction can be achieved with the benefits of precast concrete above, but the durability and resilience of this building material once erected are what set the standard higher.
Keeping Your Building Secure from Natural Disasters
Uncontrollable factors such as fire, severe storms, or earthquakes can cause a host of damages to a building. Where precast concrete stands apart is its ability to withstand these natural disasters.
Decrease Monthly Utility Costs
Whether you need a data center full of running systems, or a corporate office for your staff, controlling interior temperatures is key to maintaining utility costs.
Precast concrete absorbs and releases heat slowly, making for more efficient heating, venting, and air conditioning (HVAC) systems. Precast concrete cladding can have continuous insulation that further enhances the thermal performance of a building.
Maximize Interior Space
Load-bearing precast panels can eliminate the need for interior columns. The end result is more flexibility for interior space. If your building will inhabit staff, this extra square footage can help spread people out to feel less crowded.
Increased Economic Sustainability
Not only are the construction processes more sustainable, but precast concrete also provides economic sustainability because of its resilient nature.
Precast concrete cladding offers a longer life span and is more flexible if your structure needs to be expanded. Because of the sustainable practices in both the construction process and once the building is erected, precast concrete buildings are regularly awarded LEED certifications and meet EPD standards.
No matter where your role fits into the construction process, you can benefit from precast concrete by leveraging its speed, quality, design flexibility, environmental advantages, safety improvements, and standardization.
These benefits are particularly valuable for projects with tight timelines, complex designs, and a focus on sustainability.
Take Advantage of Precast Concrete by Connecting with a Sales Representative Early in the Construction Process
